Omnisupply
Omnisupply
OmniSupply is an enterprise MVP designed to help companies streamline operations, gain real-time visibility, and stay agile amid global supply chain disruptions.
OmniSupply is an enterprise MVP designed to help companies streamline operations, gain real-time visibility, and stay agile amid global supply chain disruptions.
OmniSupply is an enterprise MVP designed to help companies streamline operations, gain real-time visibility, and stay agile amid global supply chain disruptions.
OmniSupply is an enterprise MVP designed to help companies streamline operations, gain real-time visibility, and stay agile amid global supply chain disruptions.
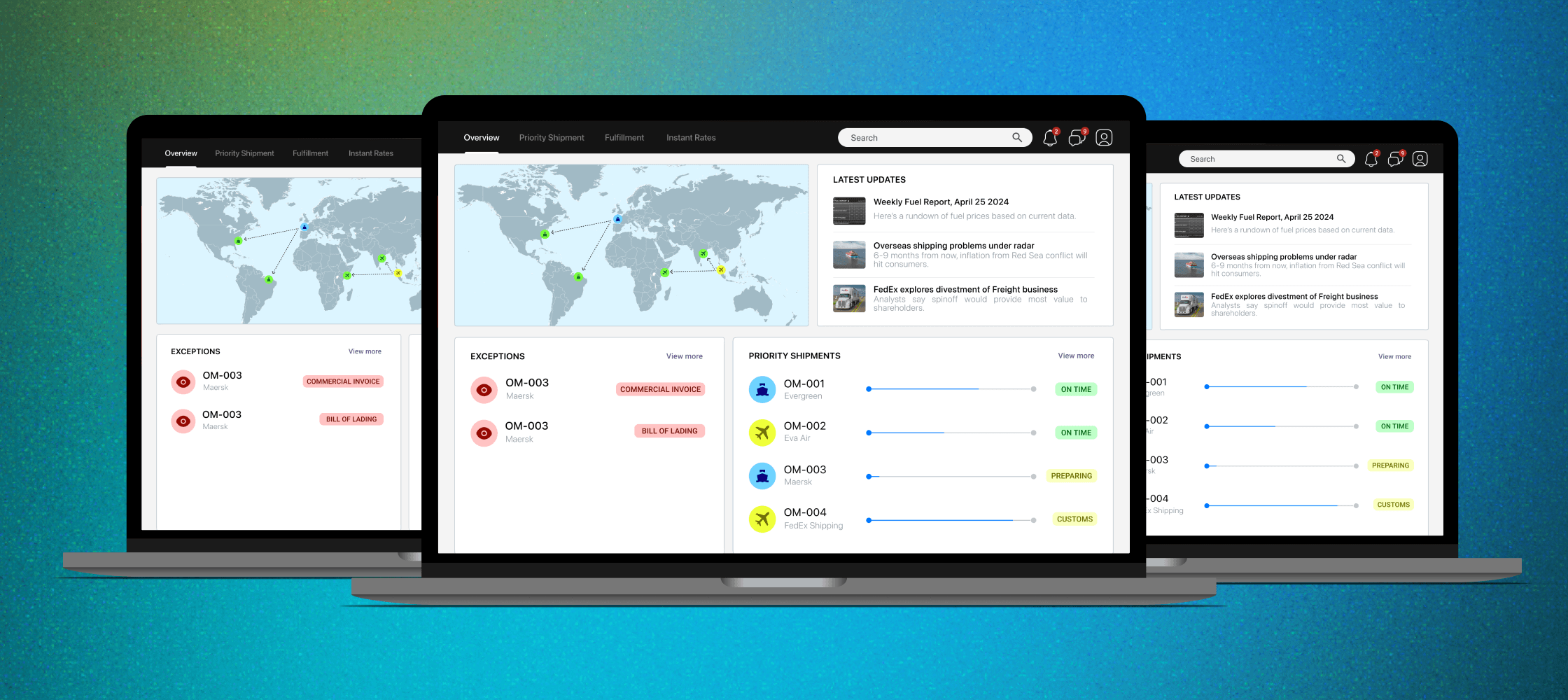
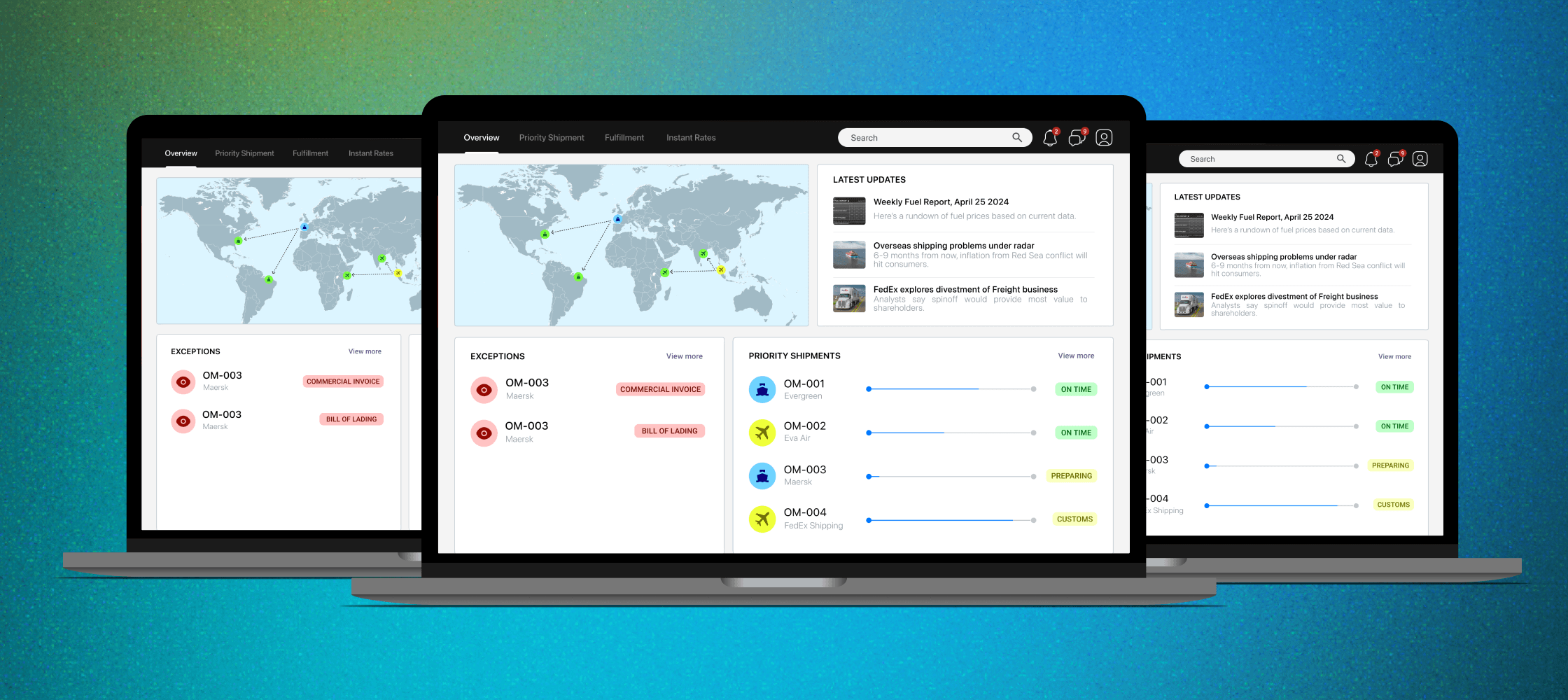
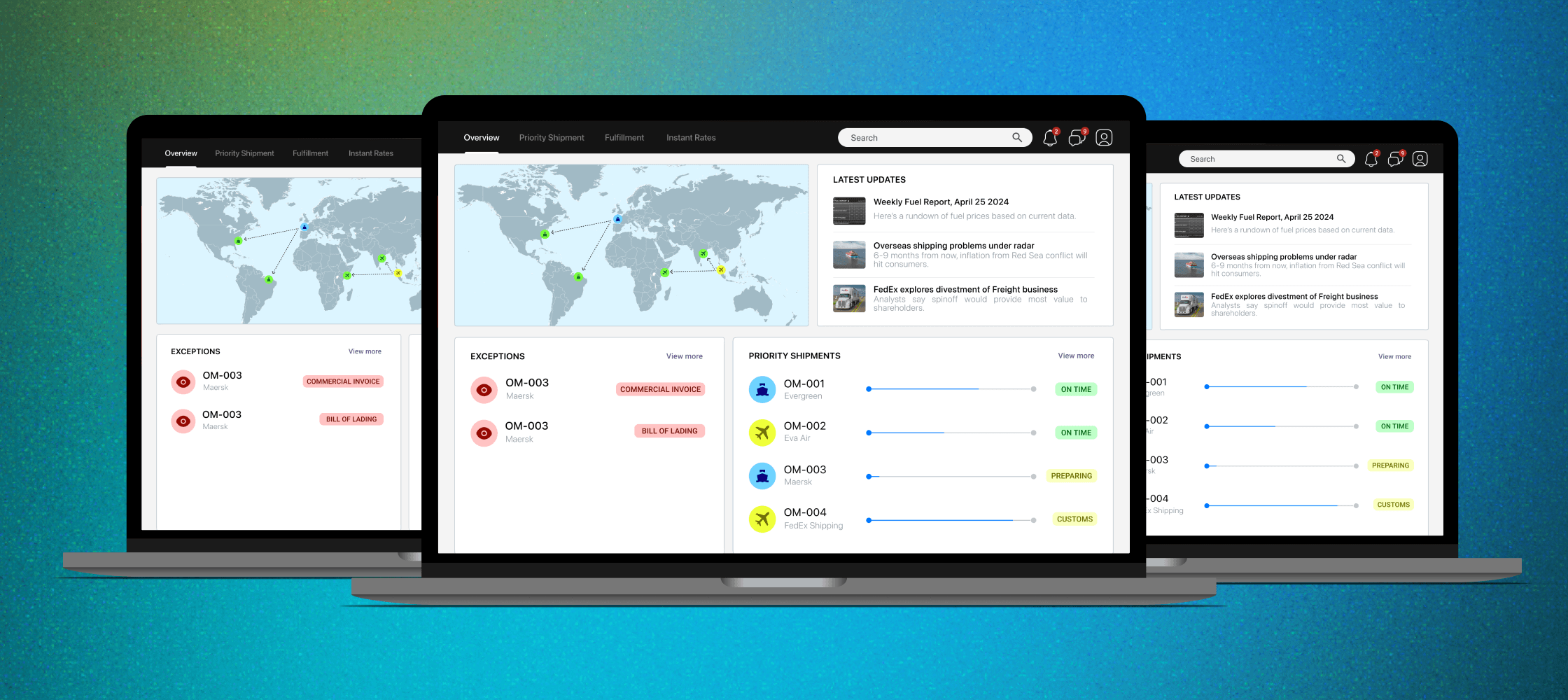
Problem
Problem
Since COVID-19, global supply chains have struggled to keep up. Delays, rising shipping costs, and outdated systems have become the norm — especially for mid-sized companies that can’t afford to build their own tools. These issues have led to serious revenue loss across a $300B market, with many businesses leaking up to 15% simply because they lack real-time visibility and modern workflows. The challenge wasn’t just about speed — it was about trust, adaptability, and keeping operations moving in a world that had changed overnight.
Since COVID-19, global supply chains have struggled to keep up. Delays, rising shipping costs, and outdated systems have become the norm — especially for mid-sized companies that can’t afford to build their own tools. These issues have led to serious revenue loss across a $300B market, with many businesses leaking up to 15% simply because they lack real-time visibility and modern workflows. The challenge wasn’t just about speed — it was about trust, adaptability, and keeping operations moving in a world that had changed overnight.
Since COVID-19, global supply chains have struggled to keep up. Delays, rising shipping costs, and outdated systems have become the norm — especially for mid-sized companies that can’t afford to build their own tools. These issues have led to serious revenue loss across a $300B market, with many businesses leaking up to 15% simply because they lack real-time visibility and modern workflows. The challenge wasn’t just about speed — it was about trust, adaptability, and keeping operations moving in a world that had changed overnight.
Problem
Since COVID-19, global supply chains have struggled to keep up. Delays, rising shipping costs, and outdated systems have become the norm — especially for mid-sized companies that can’t afford to build their own tools. These issues have led to serious revenue loss across a $300B market, with many businesses leaking up to 15% simply because they lack real-time visibility and modern workflows. The challenge wasn’t just about speed — it was about trust, adaptability, and keeping operations moving in a world that had changed overnight.
Goal
Goal
Design a single platform that gives companies real-time visibility into their shipments, centralizes pricing data across carriers and regions, and becomes the go-to hub for managing everything related to their supply chain — all in one place.
Design a single platform that gives companies real-time visibility into their shipments, centralizes pricing data across carriers and regions, and becomes the go-to hub for managing everything related to their supply chain — all in one place.
Design a single platform that gives companies real-time visibility into their shipments, centralizes pricing data across carriers and regions, and becomes the go-to hub for managing everything related to their supply chain — all in one place.
Goal
Design a single platform that gives companies real-time visibility into their shipments, centralizes pricing data across carriers and regions, and becomes the go-to hub for managing everything related to their supply chain — all in one place.
Market Research & Competitor Analysis
Market Research & Competitor Analysis
I started by mapping out the freight forwarding landscape and reviewing the few existing tools in the space. Industry reports — including those from Maersk — made it clear: supply chain software is still in the early stages of digital transformation. Even with limited platforms out there, I was able to break down what worked, what didn’t, and where user needs were being overlooked. These insights shaped our approach from day one.
I started by mapping out the freight forwarding landscape and reviewing the few existing tools in the space. Industry reports — including those from Maersk — made it clear: supply chain software is still in the early stages of digital transformation. Even with limited platforms out there, I was able to break down what worked, what didn’t, and where user needs were being overlooked. These insights shaped our approach from day one.
I started by mapping out the freight forwarding landscape and reviewing the few existing tools in the space. Industry reports — including those from Maersk — made it clear: supply chain software is still in the early stages of digital transformation. Even with limited platforms out there, I was able to break down what worked, what didn’t, and where user needs were being overlooked. These insights shaped our approach from day one.
Market Research & Competitor Analysis
I started by mapping out the freight forwarding landscape and reviewing the few existing tools in the space. Industry reports — including those from Maersk — made it clear: supply chain software is still in the early stages of digital transformation. Even with limited platforms out there, I was able to break down what worked, what didn’t, and where user needs were being overlooked. These insights shaped our approach from day one.



Requirements & User Interviews
Requirements & User Interviews
To ground the product in real-world needs, I interviewed both the founding team and supply chain professionals across Southeast Asia and the U.S. These conversations helped me unpack how legacy processes still shape daily operations — and what users actually need from modern tools. The insights were clear: they wanted more control, better visibility, and less manual coordination.
To ground the product in real-world needs, I interviewed both the founding team and supply chain professionals across Southeast Asia and the U.S. These conversations helped me unpack how legacy processes still shape daily operations — and what users actually need from modern tools. The insights were clear: they wanted more control, better visibility, and less manual coordination.
To ground the product in real-world needs, I interviewed both the founding team and supply chain professionals across Southeast Asia and the U.S. These conversations helped me unpack how legacy processes still shape daily operations — and what users actually need from modern tools. The insights were clear: they wanted more control, better visibility, and less manual coordination.
Requirements & User Interviews
To ground the product in real-world needs, I interviewed both the founding team and supply chain professionals across Southeast Asia and the U.S. These conversations helped me unpack how legacy processes still shape daily operations — and what users actually need from modern tools. The insights were clear: they wanted more control, better visibility, and less manual coordination.



Mapping the Current Journey
Mapping the Current Journey
Using insights from interviews and research, I created a journey map to visualize how different stakeholders move through the supply chain process. This helped surface time sinks and key friction points — especially where delays in one step caused costly bottlenecks down the line. The map became a critical tool for aligning the team around where design could drive the most impact.
Using insights from interviews and research, I created a journey map to visualize how different stakeholders move through the supply chain process. This helped surface time sinks and key friction points — especially where delays in one step caused costly bottlenecks down the line. The map became a critical tool for aligning the team around where design could drive the most impact.
Using insights from interviews and research, I created a journey map to visualize how different stakeholders move through the supply chain process. This helped surface time sinks and key friction points — especially where delays in one step caused costly bottlenecks down the line. The map became a critical tool for aligning the team around where design could drive the most impact.
Mapping the Current Journey
Using insights from interviews and research, I created a journey map to visualize how different stakeholders move through the supply chain process. This helped surface time sinks and key friction points — especially where delays in one step caused costly bottlenecks down the line. The map became a critical tool for aligning the team around where design could drive the most impact.



Brainstorming Solutions
Brainstorming Solutions
With clear patterns emerging from user interviews and research, I started generating ideas to address the recurring pain points in supply chain management. I focused on ways to centralize fragmented processes and reduce unnecessary complexity. These early concept sessions helped define the core features the platform needed — separating critical must-haves from nice-to-haves — and laid the foundation for a more focused, scalable product direction.
With clear patterns emerging from user interviews and research, I started generating ideas to address the recurring pain points in supply chain management. I focused on ways to centralize fragmented processes and reduce unnecessary complexity. These early concept sessions helped define the core features the platform needed — separating critical must-haves from nice-to-haves — and laid the foundation for a more focused, scalable product direction.
With clear patterns emerging from user interviews and research, I started generating ideas to address the recurring pain points in supply chain management. I focused on ways to centralize fragmented processes and reduce unnecessary complexity. These early concept sessions helped define the core features the platform needed — separating critical must-haves from nice-to-haves — and laid the foundation for a more focused, scalable product direction.
Brainstorming Solutions
With clear patterns emerging from user interviews and research, I started generating ideas to address the recurring pain points in supply chain management. I focused on ways to centralize fragmented processes and reduce unnecessary complexity. These early concept sessions helped define the core features the platform needed — separating critical must-haves from nice-to-haves — and laid the foundation for a more focused, scalable product direction.
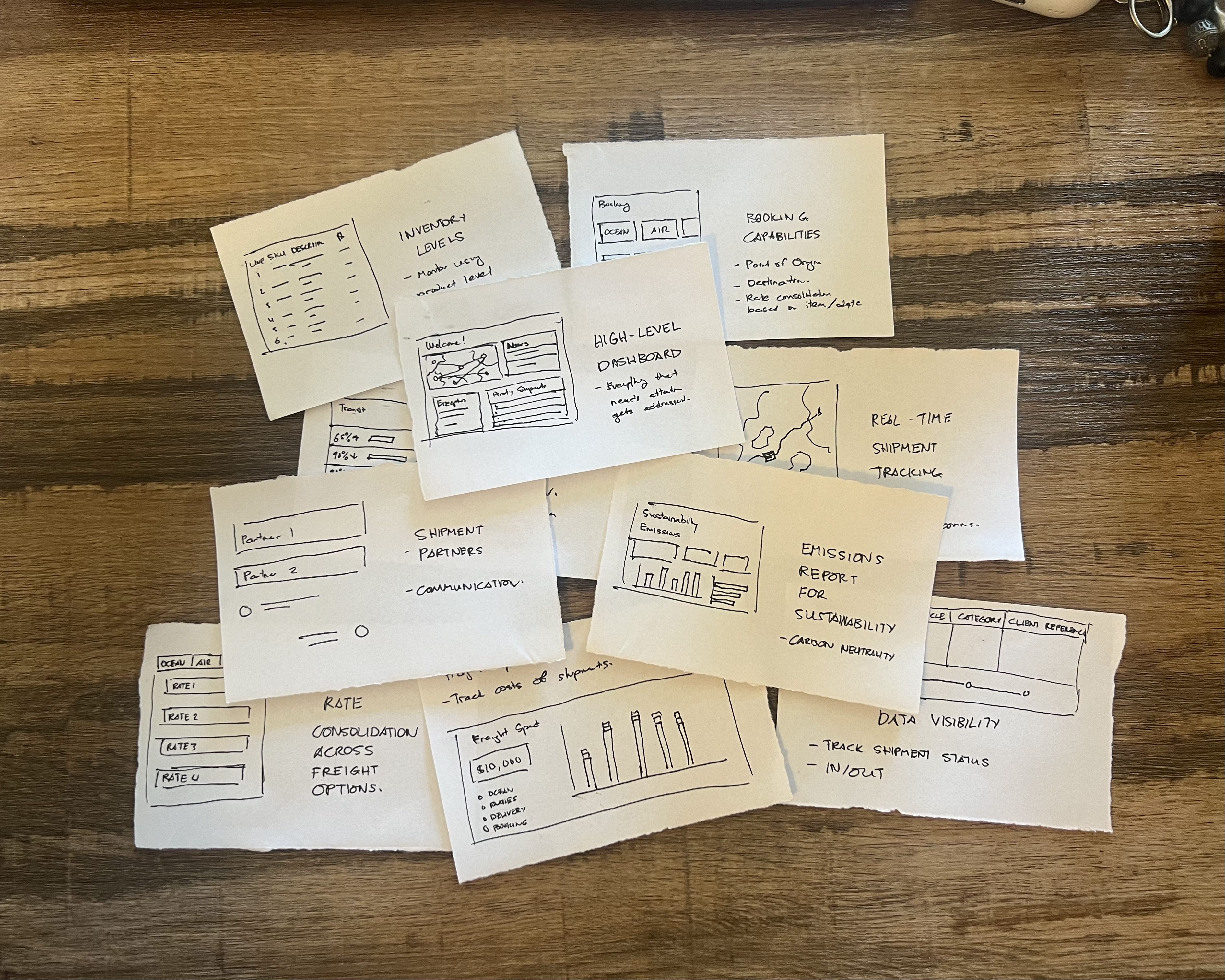
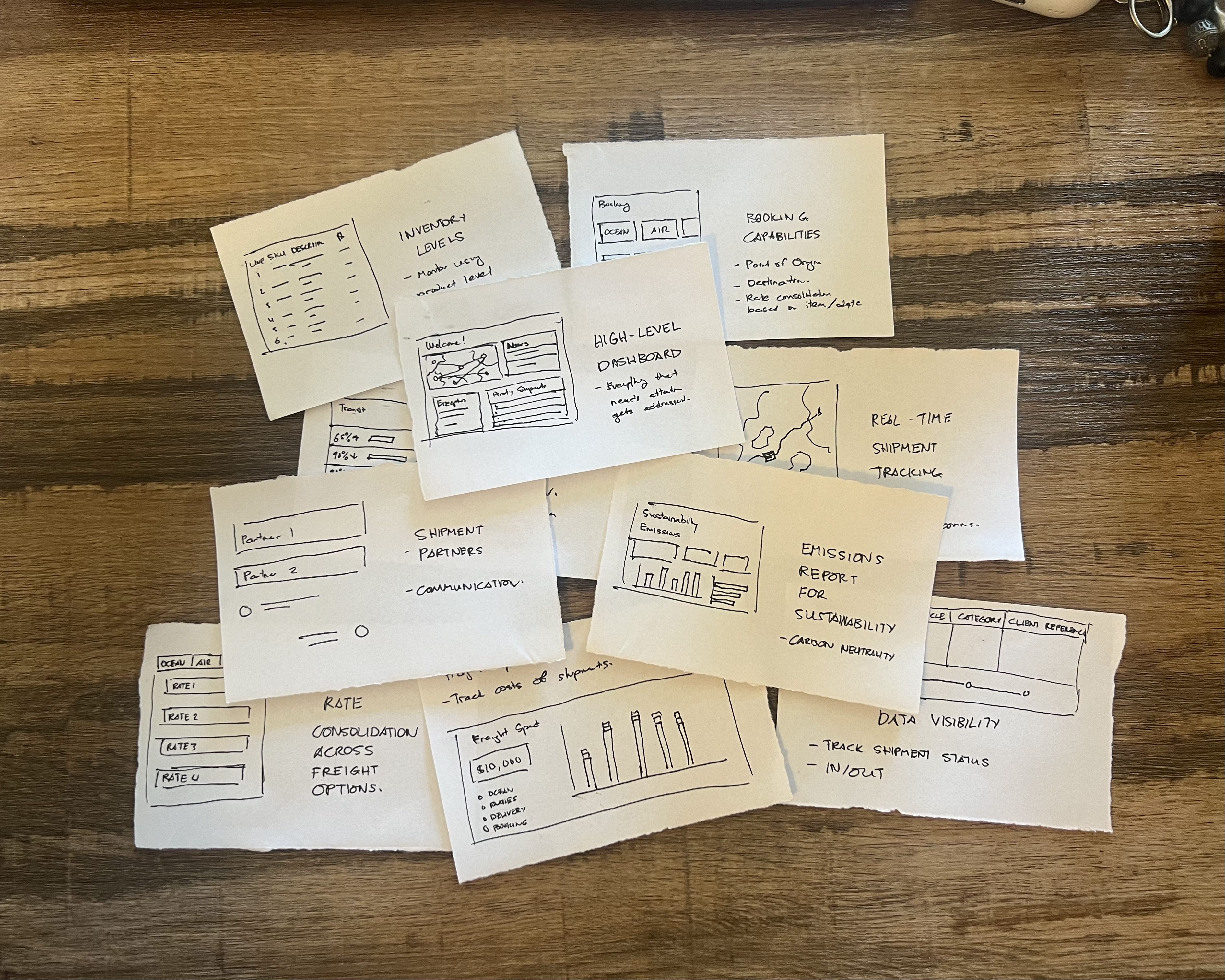
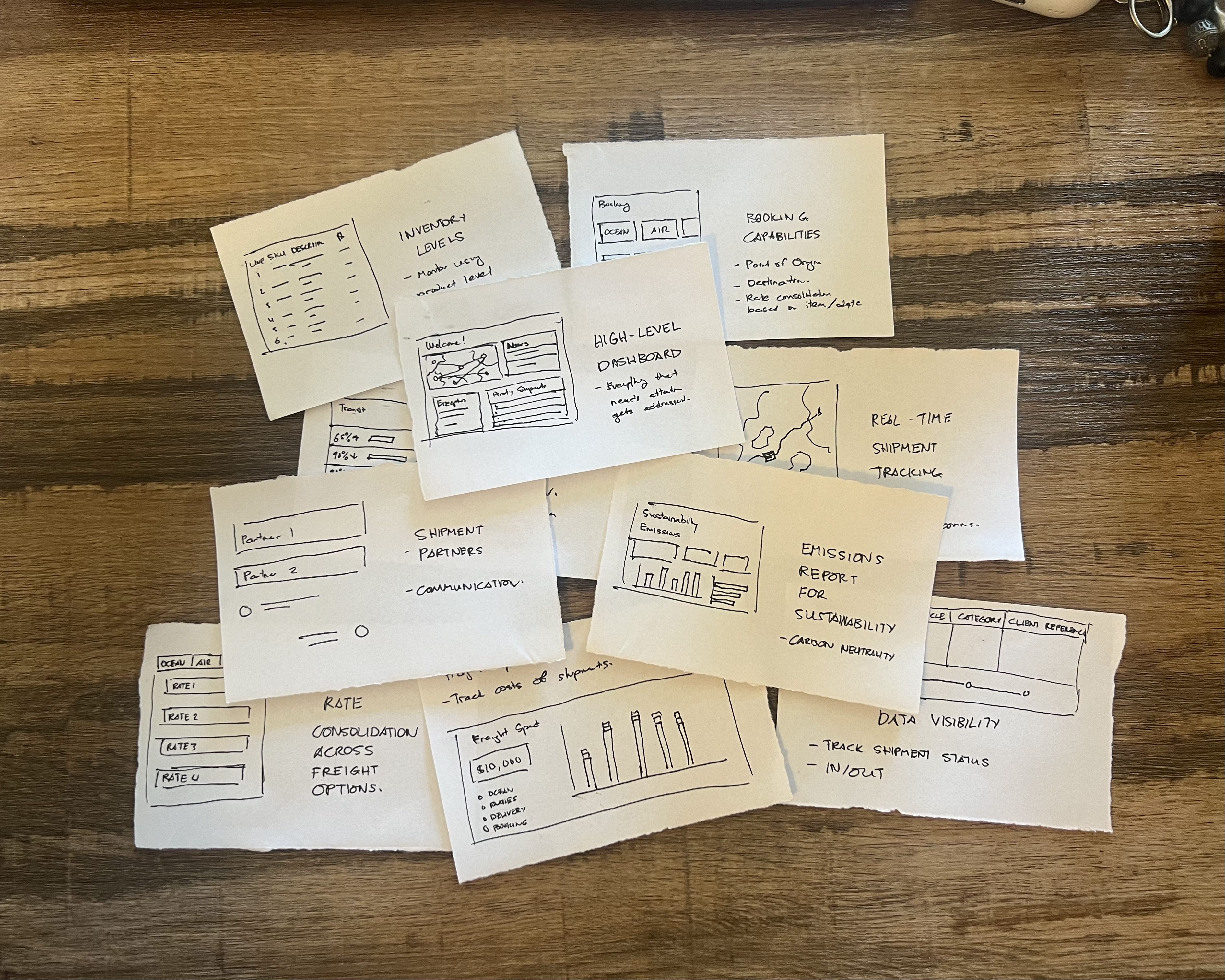
Sketching & Early Concepts
Sketching & Early Concepts
I began the design process with quick sketches that combined key features and components based on user feedback and market insights. This phase was all about exploring how to present complex data clearly — testing different layouts, interactions, and content hierarchies to find the most intuitive way to surface the right information at the right time.
I began the design process with quick sketches that combined key features and components based on user feedback and market insights. This phase was all about exploring how to present complex data clearly — testing different layouts, interactions, and content hierarchies to find the most intuitive way to surface the right information at the right time.
I began the design process with quick sketches that combined key features and components based on user feedback and market insights. This phase was all about exploring how to present complex data clearly — testing different layouts, interactions, and content hierarchies to find the most intuitive way to surface the right information at the right time.
Sketching & Early Concepts
I began the design process with quick sketches that combined key features and components based on user feedback and market insights. This phase was all about exploring how to present complex data clearly — testing different layouts, interactions, and content hierarchies to find the most intuitive way to surface the right information at the right time.
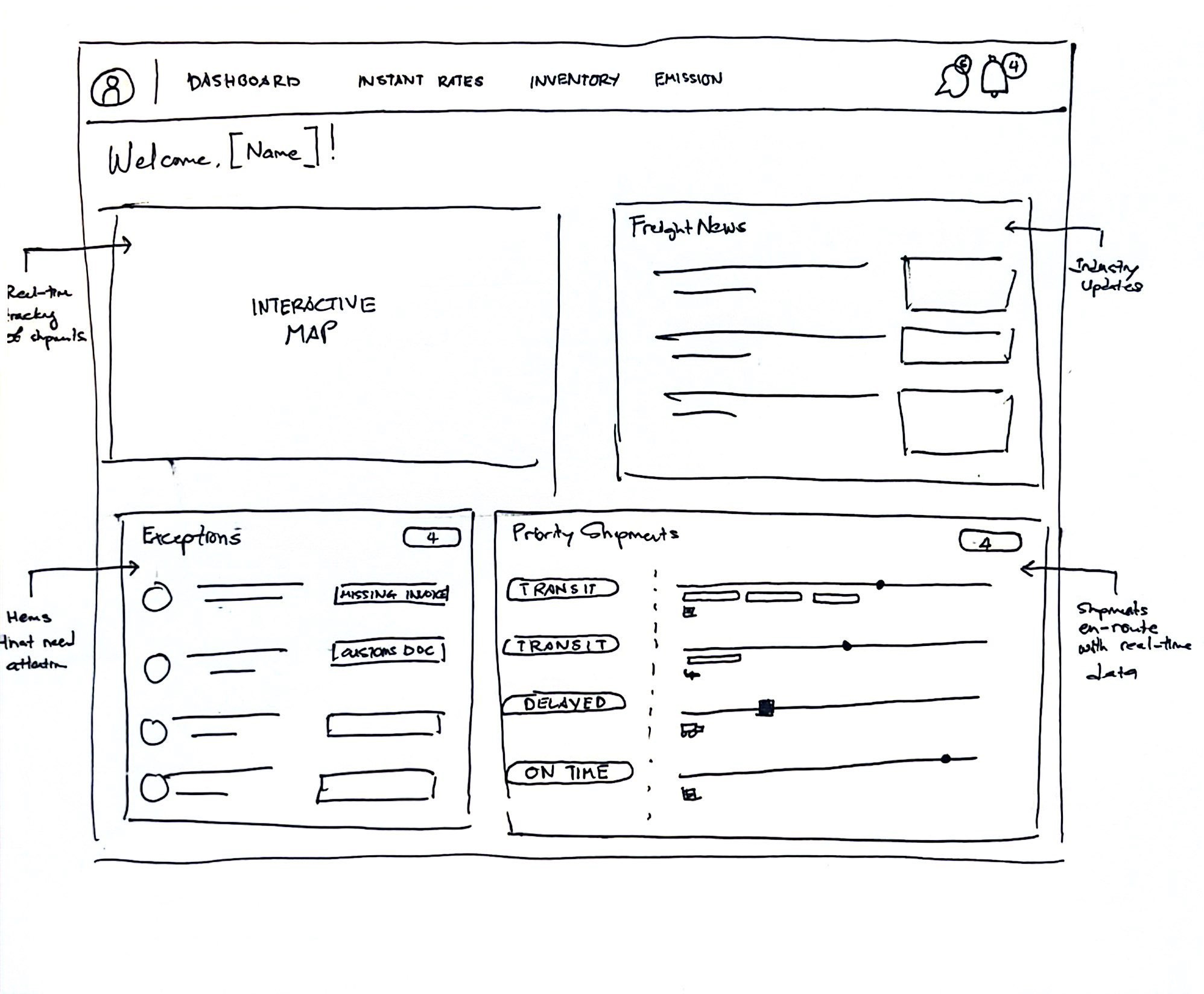
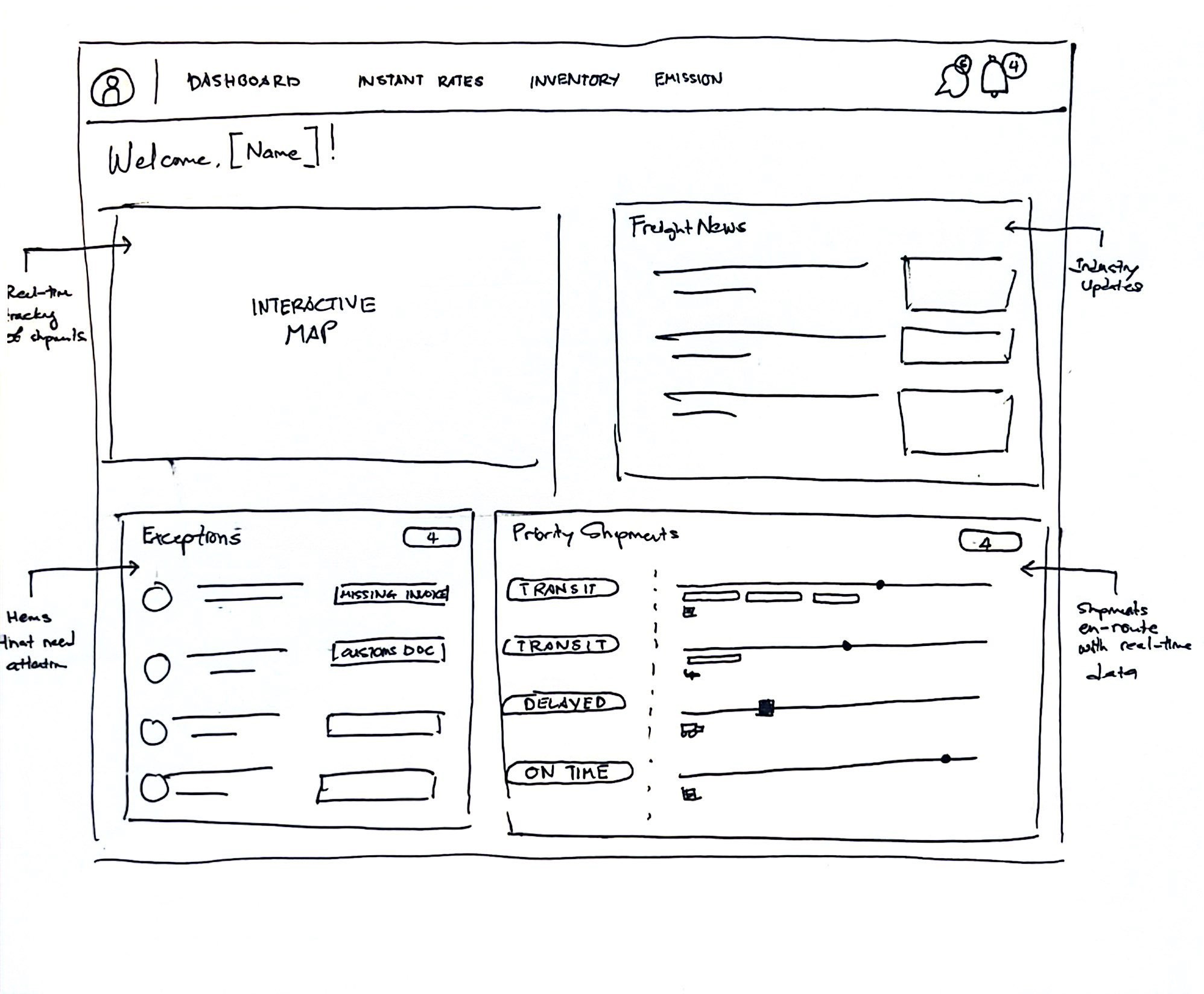
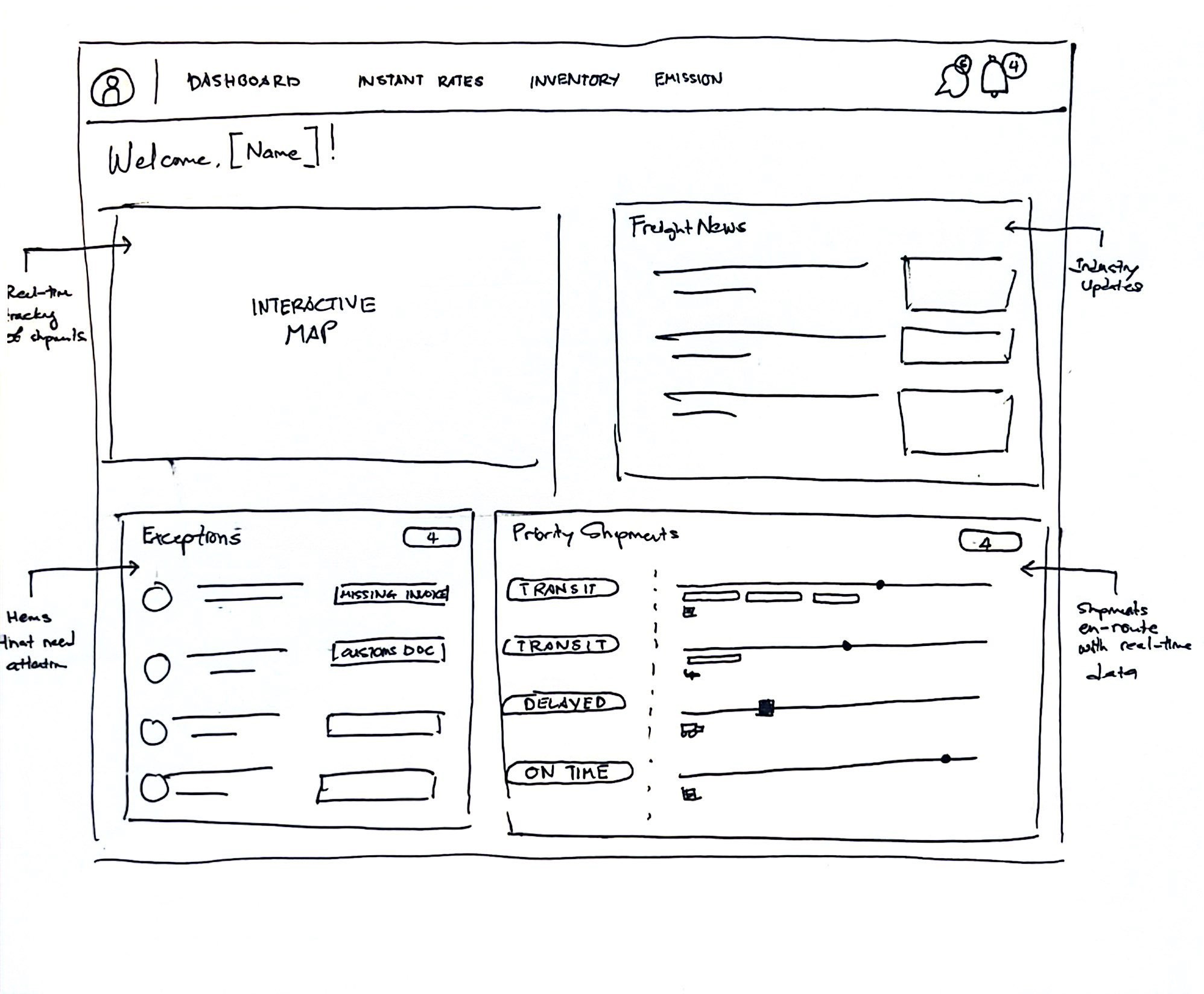
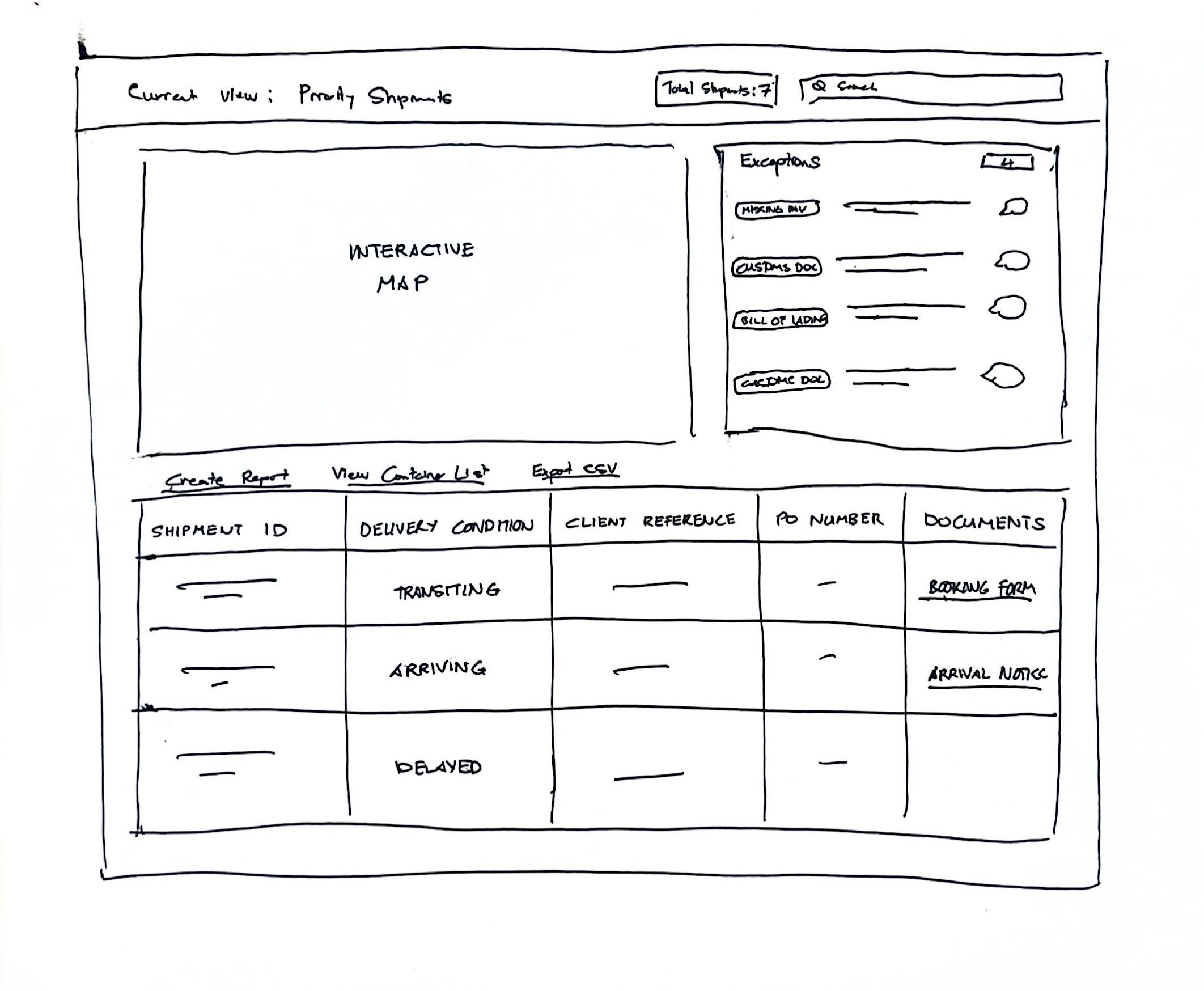
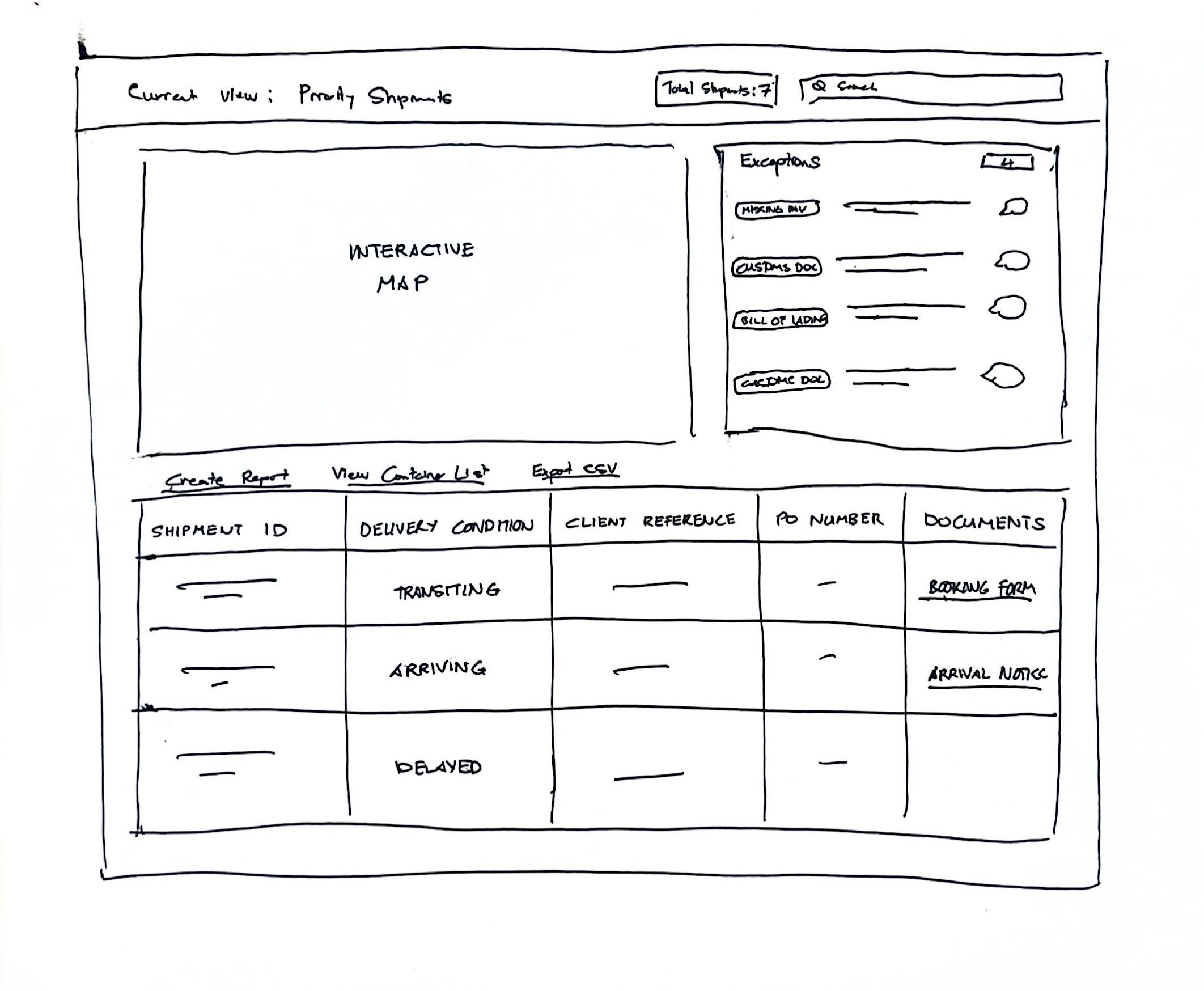
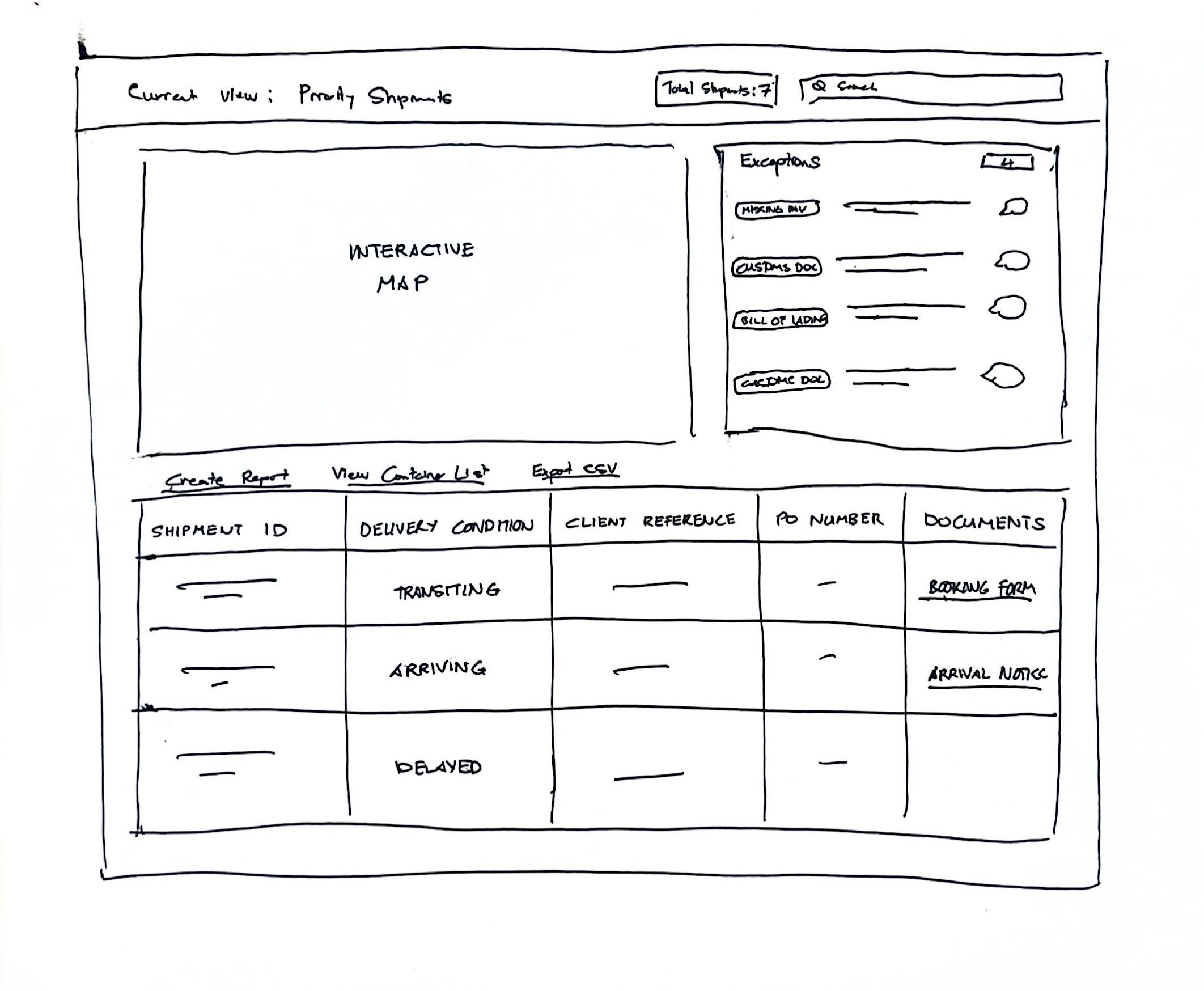
Wireframing the Experience
Wireframing the Experience
After sketching out the core ideas, I moved into low-fidelity wireframes in Figma to bring structure to the concept. This phase helped translate rough thinking into tangible layouts, giving shape to the app’s key flows and functionality. Wireframing allowed me to rapidly test different interaction models and information hierarchies — ensuring the design was usable, scalable, and grounded in user needs before moving into high-fidelity execution.
After sketching out the core ideas, I moved into low-fidelity wireframes in Figma to bring structure to the concept. This phase helped translate rough thinking into tangible layouts, giving shape to the app’s key flows and functionality. Wireframing allowed me to rapidly test different interaction models and information hierarchies — ensuring the design was usable, scalable, and grounded in user needs before moving into high-fidelity execution.
After sketching out the core ideas, I moved into low-fidelity wireframes in Figma to bring structure to the concept. This phase helped translate rough thinking into tangible layouts, giving shape to the app’s key flows and functionality. Wireframing allowed me to rapidly test different interaction models and information hierarchies — ensuring the design was usable, scalable, and grounded in user needs before moving into high-fidelity execution.
Wireframing the Experience
After sketching out the core ideas, I moved into low-fidelity wireframes in Figma to bring structure to the concept. This phase helped translate rough thinking into tangible layouts, giving shape to the app’s key flows and functionality. Wireframing allowed me to rapidly test different interaction models and information hierarchies — ensuring the design was usable, scalable, and grounded in user needs before moving into high-fidelity execution.



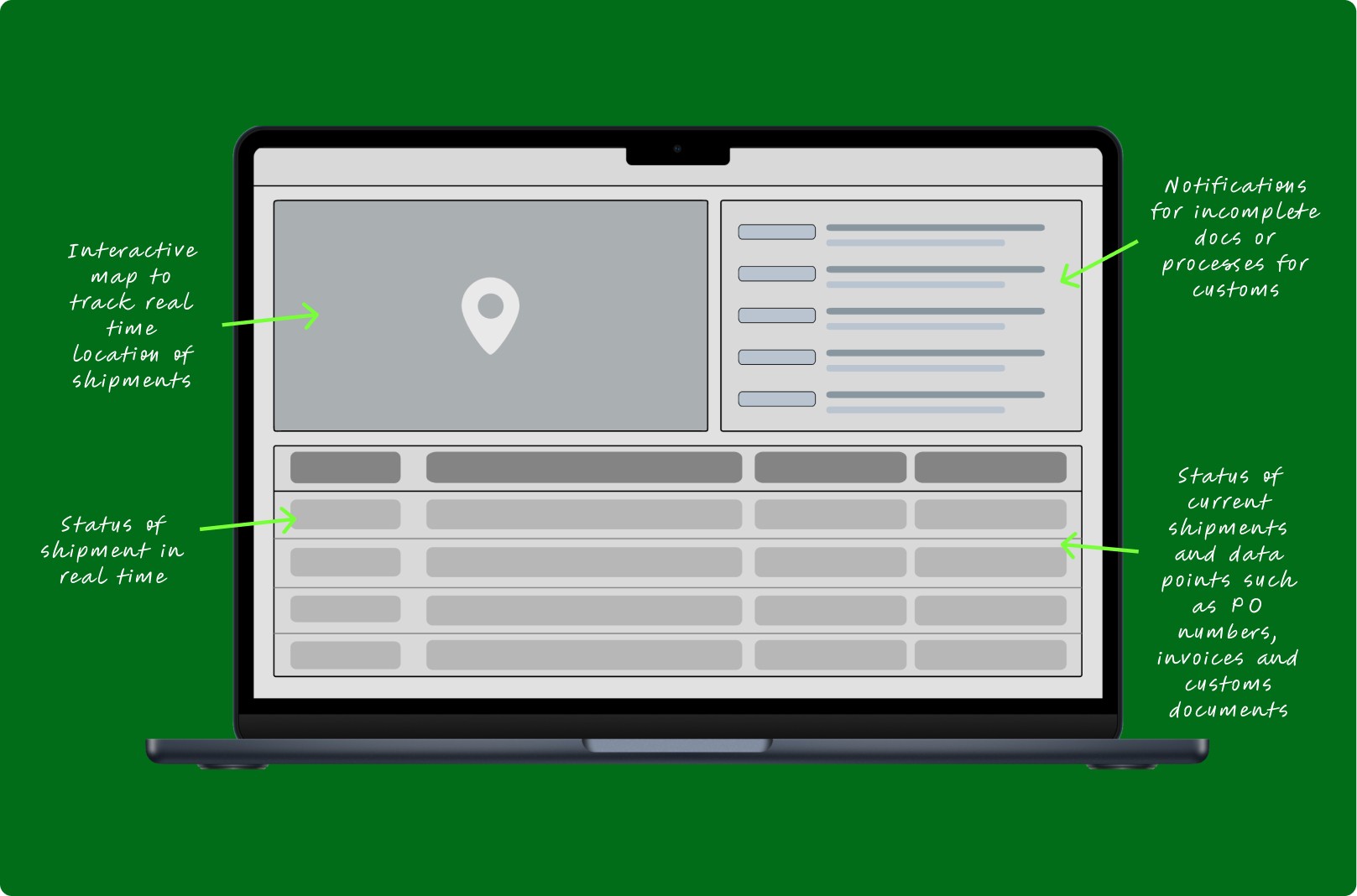
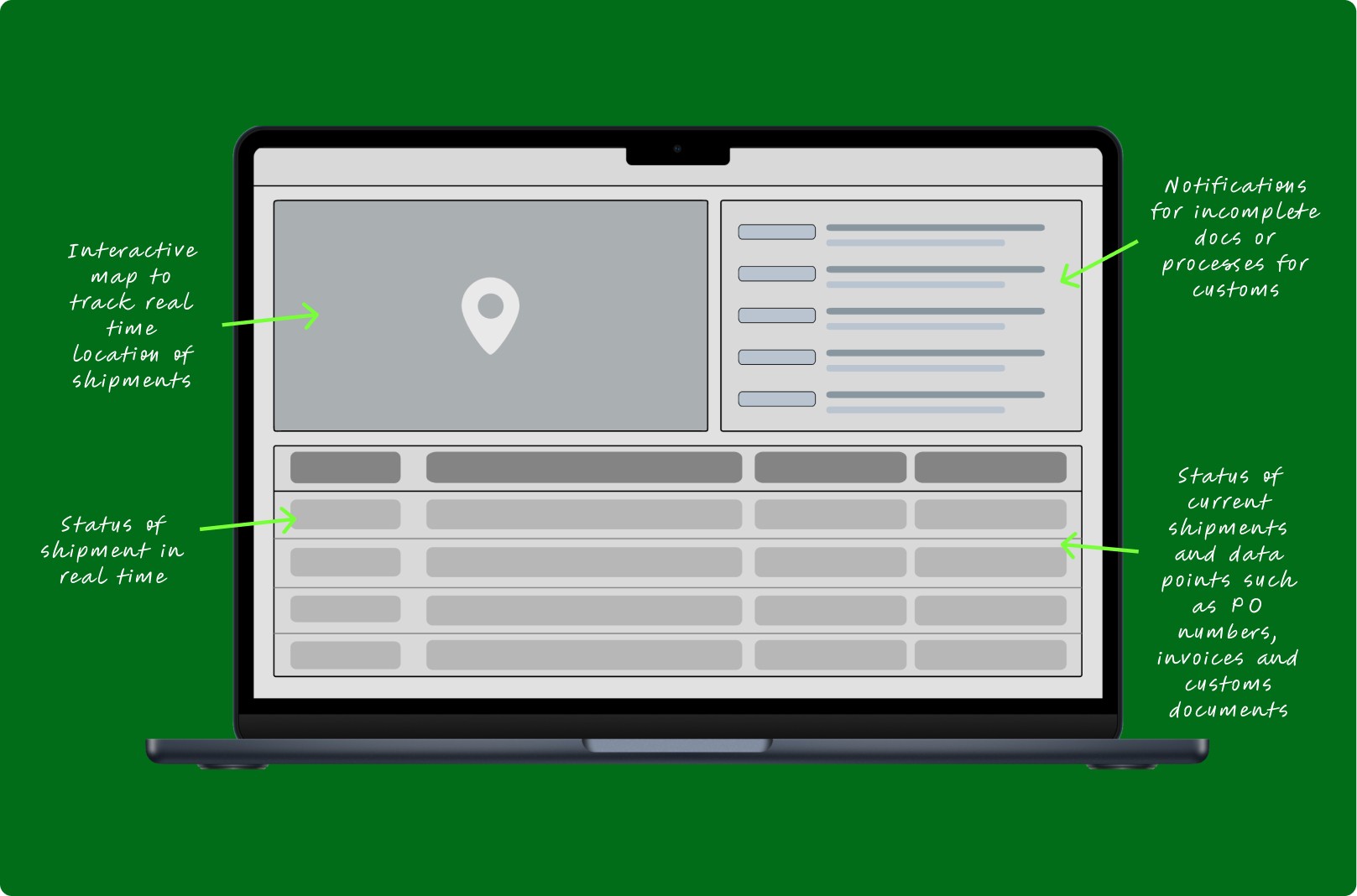
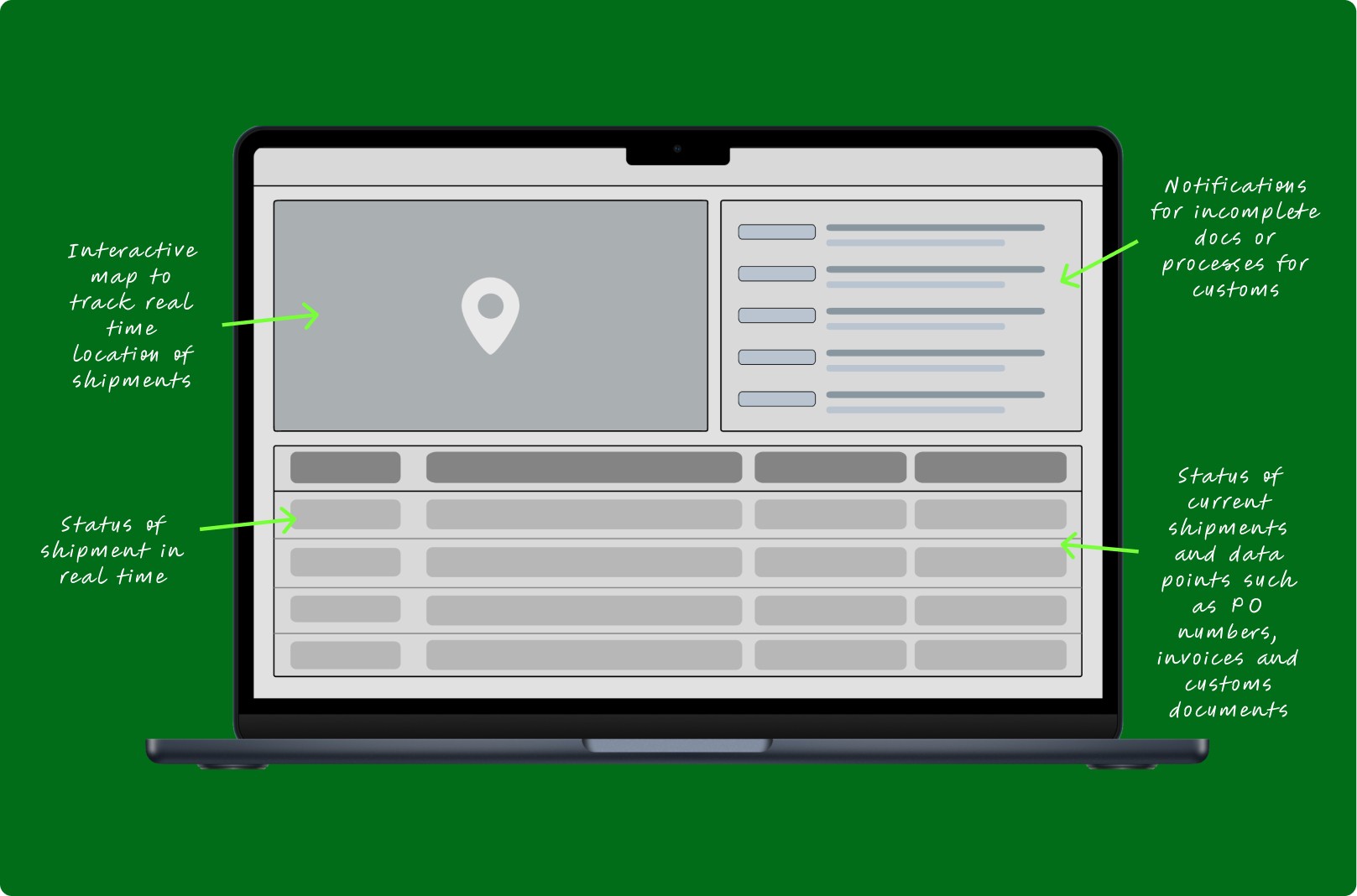
OUTCOME: CENTRALIZED COMMS & DOCUMENTATION
OUTCOME: CENTRALIZED COMMS & DOCUMENTATION
Before OmniSupply, supply chain managers had to juggle scattered emails, spreadsheets, and manual updates just to keep shipments on track. By centralizing communication and documentation, the platform now enables managers to coordinate with shipping partners, resolve issues, and verify compliance — all in one place. Real-time tracking and a unified interaction history bring transparency, reduce back-and-forth, and streamline decision-making across the entire shipment lifecycle.
Before OmniSupply, supply chain managers had to juggle scattered emails, spreadsheets, and manual updates just to keep shipments on track. By centralizing communication and documentation, the platform now enables managers to coordinate with shipping partners, resolve issues, and verify compliance — all in one place. Real-time tracking and a unified interaction history bring transparency, reduce back-and-forth, and streamline decision-making across the entire shipment lifecycle.
Before OmniSupply, supply chain managers had to juggle scattered emails, spreadsheets, and manual updates just to keep shipments on track. By centralizing communication and documentation, the platform now enables managers to coordinate with shipping partners, resolve issues, and verify compliance — all in one place. Real-time tracking and a unified interaction history bring transparency, reduce back-and-forth, and streamline decision-making across the entire shipment lifecycle.
OUTCOME: CENTRALIZED COMMS & DOCUMENTATION
Before OmniSupply, supply chain managers had to juggle scattered emails, spreadsheets, and manual updates just to keep shipments on track. By centralizing communication and documentation, the platform now enables managers to coordinate with shipping partners, resolve issues, and verify compliance — all in one place. Real-time tracking and a unified interaction history bring transparency, reduce back-and-forth, and streamline decision-making across the entire shipment lifecycle.
OUTCOME: REAL TIME DATA VISIBILITY
OUTCOME: REAL TIME DATA VISIBILITY
For finance teams managing complex supply chain operations, tracking freight spend — especially duties and hidden fees — can be a black box. OmniSupply changes that by offering real-time visibility into every shipment and its associated costs. Teams can now monitor expenses down to the last cent, reducing financial ambiguity and enabling more accurate budgeting, forecasting, and operational oversight.
For finance teams managing complex supply chain operations, tracking freight spend — especially duties and hidden fees — can be a black box. OmniSupply changes that by offering real-time visibility into every shipment and its associated costs. Teams can now monitor expenses down to the last cent, reducing financial ambiguity and enabling more accurate budgeting, forecasting, and operational oversight.
For finance teams managing complex supply chain operations, tracking freight spend — especially duties and hidden fees — can be a black box. OmniSupply changes that by offering real-time visibility into every shipment and its associated costs. Teams can now monitor expenses down to the last cent, reducing financial ambiguity and enabling more accurate budgeting, forecasting, and operational oversight.
OUTCOME: REAL TIME DATA VISIBILITY
For finance teams managing complex supply chain operations, tracking freight spend — especially duties and hidden fees — can be a black box. OmniSupply changes that by offering real-time visibility into every shipment and its associated costs. Teams can now monitor expenses down to the last cent, reducing financial ambiguity and enabling more accurate budgeting, forecasting, and operational oversight.
OUTCOME: FREIGHT RATES
OUTCOME: FREIGHT RATES
In today’s volatile economic landscape, supply chain resilience depends on flexibility. OmniSupply empowers companies to quickly compare freight rates across regions and providers, making it easier to pivot when disruptions arise. By surfacing real-time alternatives, the platform helps teams avoid delays, reduce costs, and keep operations running — no matter what challenges emerge.
In today’s volatile economic landscape, supply chain resilience depends on flexibility. OmniSupply empowers companies to quickly compare freight rates across regions and providers, making it easier to pivot when disruptions arise. By surfacing real-time alternatives, the platform helps teams avoid delays, reduce costs, and keep operations running — no matter what challenges emerge.
In today’s volatile economic landscape, supply chain resilience depends on flexibility. OmniSupply empowers companies to quickly compare freight rates across regions and providers, making it easier to pivot when disruptions arise. By surfacing real-time alternatives, the platform helps teams avoid delays, reduce costs, and keep operations running — no matter what challenges emerge.
OUTCOME: FREIGHT RATES
In today’s volatile economic landscape, supply chain resilience depends on flexibility. OmniSupply empowers companies to quickly compare freight rates across regions and providers, making it easier to pivot when disruptions arise. By surfacing real-time alternatives, the platform helps teams avoid delays, reduce costs, and keep operations running — no matter what challenges emerge.
KEY FINDINGS
KEY FINDINGS
23%

OPS EFFICIENCY
Quicker issue resolution between clients and shipping partners.
Quicker issue resolution between clients and shipping partners.
30%

BUDGETING ERRORS
Precise financial tracking and informed decision-making for finance teams.
Precise financial tracking and informed decision-making for finance teams.
21%

LATE SHIPMENTS
Mimimal disruptions in the supply chain experience through real-time tracking.
Mimimal disruptions in the supply chain experience through real-time tracking.
23%

OPS EFFICIENCY
Quicker issue resolution between clients and shipping partners.
30%

BUDGETING ERRORS
Precise financial tracking and informed decision-making for finance teams.
21%

LATE SHIPMENTS
Mimimal disruptions in the supply chain experience through real-time tracking.
23%

OPS EFFICIENCY
Quicker issue resolution between clients and shipping partners.
30%

BUDGETING ERRORS
Precise financial tracking and informed decision-making for finance teams.
21%

LATE SHIPMENTS
Mimimal disruptions in the supply chain experience through real-time tracking.
More Work More Work
More Work More Work
©2024 ALL RIGHTS RESERVED.
GO BACK TO TOP
©2024 ALL RIGHTS RESERVED.
GO BACK TO TOP